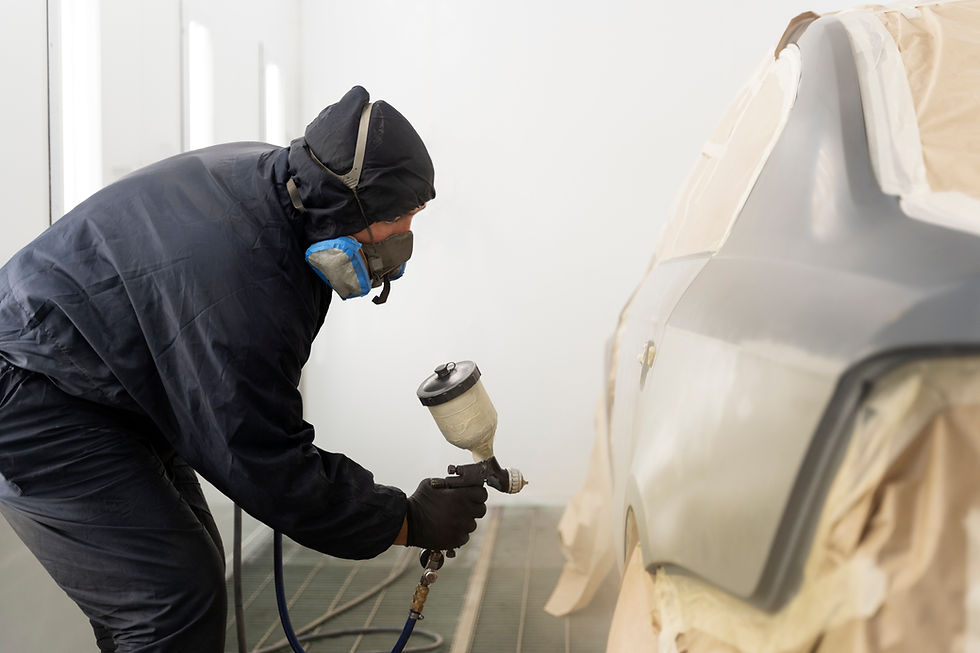
Everyone wants a flawless, durable, and long-lasting paint job, and powder coating is a popular choice that perfectly meets these expectations. With its exceptional properties—high durability, resistance to scratches, UV rays, rain, and chemicals—powder coating is also an eco-friendly option. That’s why it’s commonly used on everything from luxury cars and household appliances to furniture and architectural structures.
However, powder coating isn’t as simple as it seems. Behind its impeccable finish lies a meticulous process that requires careful attention to detail. A minor mistake can lead to disastrous results, turning a professional-grade job into a botched mess that needs to be redone—wasting time, money, and effort.
This article explores the common pitfalls in powder coating that beginners often overlook, which can ruin the final outcome. We’ll also provide essential tips to help you
Things to Watch Out for in Powder Coating
Powder coating is a widely used finishing technique that offers outstanding advantages. However, much like building a house, a strong foundation is crucial. No matter how high-quality the materials are, a poor foundation can lead to structural failure. Similarly, in powder coating, neglecting critical steps—from surface preparation and paint selection to application and curing—can result in defects like peeling, uneven color, or weak adhesion.
Let’s take a closer look at the most common issues and how to prevent them.
1. Uneven or Imperfect Surface Preparation
A smooth and clean surface is fundamental to achieving a high-quality powder-coated finish. Imagine painting over dents, scratches, or rough textures—these imperfections will remain visible, resulting in an unsightly finish. Moreover, uneven surfaces can cause the powder to accumulate in depressions while appearing thin on raised areas, leading to inconsistent color shades. Scratches, dents, and cracks can also promote rust formation, which accelerates paint deterioration.
How to prevent this:
Ensure the surface is clean, free of dust, grease, and rust before coating.
Smooth out imperfections using sanding, grinding, or putty application as needed.
If the surface is significantly damaged, consider applying a primer to conceal defects and enhance adhesion.
Select the right type of powder coating; for example, textured finishes can help mask minor imperfections better than smooth coatings.
2. Failure to Clean the Surface Before Coating
Skipping the cleaning step before powder coating is a serious mistake that can drastically impact adhesion. Think of it like painting a dirty wall—paint won’t stick properly, leading to premature peeling and an unappealing finish.
Powder coating adheres to surfaces using electrostatic attraction, meaning any contaminants such as dust, oil, grease, rust, or chemical residues can interfere with adhesion. This can result in:
The coating peeling off in layers.
Small particles creating bumps, dimples, or uneven spots on the surface.
Oil, grease, or moisture causing bubbles under the coating, which may eventually burst and lead to peeling.
Chemical residues reacting with the powder, leading to discoloration or stains.
Rust gradually corroding the surface beneath the coating, reducing its lifespan.
How to prevent this:
Always remove dust, dirt, and debris using compressed air, brushes, or clean cloths before coating.
Use appropriate cleaning agents based on the material and the type of contamination, such as degreasers or rust removers.
For stubborn dirt or rust, use sandpaper, wire brushes, or other mechanical tools to prepare the surface thoroughly.
3. Inconsistent Curing Temperature
Maintaining a consistent curing temperature is crucial to achieving a flawless powder-coated finish. Powder coating particles melt and bond to the surface when exposed to heat, and uniform heating ensures an even, durable finish.
If the temperature is uneven:
Overheated areas may burn, crack, or change color.
Underheated areas may not fully cure, resulting in a rough or patchy appearance.
Improper temperature control can weaken adhesion, making the coating prone to peeling.
Temperature variations can create internal stress within the coating, leading to cracks over time.
How to prevent this:
Use a high-quality curing oven with even heat distribution.
Regularly check temperature settings to ensure consistency.
Monitor curing times according to the manufacturer’s specifications.
Avoid overloading the oven, as overcrowding can lead to temperature variations.
By being mindful of these common mistakes and taking the necessary precautions, you can ensure that your powder coating projects turn out beautifully—smooth, durable, and free from defects. Whether you’re coating industrial parts, furniture, or automotive components, proper preparation, application, and curing will guarantee professional-grade results.
And if you're looking for experts in laser cutting and metal fabrication to prepare your workpieces for powder coating, Pailin Laser Metal (PLM) is ready to serve you with state-of-the-art technology, high precision, and extensive experience. Rest assured in the quality of workpieces that are perfectly prepared for coating. Contact PLM today and experience superior metal fabrication quality.
Comments